The Saudi Aramco-KAIST CO2 Management Center (Director: Prof. Jay H. Lee in the Department of Chemical Engineering) was started to provide innovative and systematic solutions for CO2 capture, conversion, storage, and emission technology to reduce anthropogenic CO2 emissions. In particular, we are developing new technologies to transform CO2 into valuable products in economically and environmentally feasible ways. Systems technology are being employed to assess the economics and CO2 life cycle footprint for the methods. It is also contributing to the development of a workforce equipped with knowledge and skill sets in the general areas of energy and sustainability.
CO2 emissions are regarded as one of the main causes of global warming by the greenhouse effect. Numerous attempts have been carried out for CO2 capture and storage, but an eventual resolution may be the direct use of CO2 to produce more useful chemicals. Therefore, the activation and reduction of CO2 are the ultimate goals of CO2 management. However, it is very difficult to overcome the activation energy barrier of C-O bond cleavage, and either high reaction temperature or large electrochemical potentials are often required. To this end, photocatalytic conversion seems to be a promising process under ambient conditions by harnessing solar energy, which makes it economical and environmentally benign.
There is a general consensus in the science and industrial communities that CO2 is one of the most inexpensive and renewable carbon resources, not only from green chemistry and environmental aspects, but also from the huge potential of industrial cost-effective resources. Thus, the development of efficient catalytic processes for the utilization of CO2 will have a tremendous direct impact in industrial chemistry. However, given the thermodynamics and kinetics of CO2 catalytic reactions, it is a major challenge to design, evaluate, and search for more efficient catalysts for CO2 -insertion chemical transformations. On the other hand, formic acid and CO are two major products from CO2 conversion. However, producing such a cheap chemical feedstock cannot be a practical solution due to the weak economic impact on the current industry. Therefore, the direct conversion of CO2 into more valuable products such as organic carbonates and isocyanate is required. In fact, organic poly- and cyclic-carbonates are widely employed for chemical, industrial, and pharmaceutical applications. According to a recent report, the world market of organic carbonates is estimated to be around $10 billion dollars, with production of over 5 million tons per year. At present, 10% of the total products are being made through CO2 conversion. Thus, development of more effective catalysts is essential.
Isocyanate is another attractive chemical because it is a valuable synthetic precursor in polymer chemistry. The global market for 2,4-toluene diisocyanate (TDI) or methylene 4,4'-diphenyl diisocyanide (MDI) accounts for 95% of isocyanate demand and is currently estimated at around $2.0 billion dollars and the market continues to grow due to its high demand as a starting material for various polyurethanes. Given the usage of highly toxic phosgene and production of corrosive materials such as HCl, alternative synthetic routes for the isocyanate industry are currently under investigation. As such, a new method is currently needed directly convert CO2 into desired isocyanate.
Several catalysts, including metal oxides and coordination metal complexes, have been reported for the synthesis of cyclic carbonates by insertion of CO2 with epoxides. While some of these studies have shown good conversion and selectivity, most of the catalysts have at least one or two issues: instability of the catalyst, mass production, expensive solvent and additives, high temperature and pressure, slow reaction kinetics, and reusability. Metal-salen complexes incorporating Cr(III), Co(III), or Al(III) are known to be effective.
Polyoxometalates are also a good candidate because of their catalytic flexibility for various applications.
Through the overall mineralization system, the hydrolysis of CO2 is the first step of the rate-limiting reaction during the formation of mineralization such that the absorbents that are initially contained in the system can selectively capture CO2. In this research, the biotic (e.g., carbonic anhydrase (CA) and bio-inspired adhesives) as well as abiotic absorbents (e.g., alkali and/or amine based chemicals) are investigated. In the next step, the carbonate (CO32-) and bicarbonate (HCO3-) ions cause precipitation when only the positive counter ions (e.g., Na+, K+, Mg2+, and Ca2+) are transferred by the electrical attraction. Herein, any salt-containing solution, including such as industrial waste, sea water, even brine with low concentration, can serve as a counter-ion supplier. The minerals recovered from this electrolytic system contain both the carbonate and bicarbonate ions; however, the components change their form mutually according to the simple treatment of pH and temperature as necessary. Consequently, our approach can eliminate CO2 from the flue gas (typically 10~15%) and at the same time produce valuable products for industrial applications. Also, the pure gas, (e.g. chlorine (Cl2) gas, and hydrogen gas (O2) on the anodic part, and hydrogen (H+) gas on the cathodic part) produced by the reaction of oxidation/reduction on the electrode can also be recovered, adding to the economic benefits.
Along with the development of electrolytic system, due to the ever-changing economic variables (e.g. cost of raw material, transport fee, exchange rate, and taxes), there is a need to use optimize the systems using simulations. In addition, the adaption of experimental results into a systemic approach is necessary. The electrolytic system is a key process in terms of maintaining alkalinity for CO2 hydrolysis and supplying sufficient counter ions; nevertheless, the system has a bottleneck due to the inevitable cost incurred by usingelectric energy, and sensitive effects caused by scale-up. Therefore, numerical optimization of this electrolytic system is necessary to reduce the operating cost as well as investments, furthermore, the capacity of CO2 in mineralization according with the operation time also can be predicted.
APUs for Heavy-duty Trucks
Heavy-duty trucks are widely used around the world to deliver large volumes of goods between distant areas. To meet the truck drivers' needs, many conveniences such as air conditioners, refrigerators, and cooking appliances need to be provided inside the cabs of heavy-duty trucks. In order to use these electrical appliances, truck drivers usually idle the engine to produce electricity. However, engine idling has several disadvantages including noise and air pollution. Diesel engines produce noise and vibration during their operation even when they are operating at a low RPM. With the noise and vibration, the nighttime use of diesel engines is restricted. Engine idling also produces enormous amounts of pollutants such as NOx and PMs. Additionally, fuel efficiency is very low during idling compared to normal driving conditions. Therefore, some states in the U.S. have started to prohibit engine idling by law. It is clear that another way to produce electrical energy is required for heavy-duty trucks.
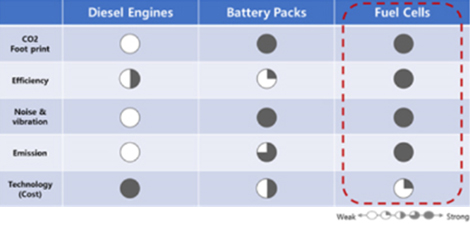
The Development of a Diesel-based SOFC Unit
There is an 'eco-friendly' way to achieve this goal. A diesel-powered Auxiliary Power Unit (APU) system is being proposed as a solution that utilizes more robust metal-supported Solid Oxide Fuel Cell (SOFC) technology. Metal-supported SOFCs is being investigated by Professor Joongmyeon Bae's group at KAIST and its associate company, H&Power in an effort to overcome the intrinsic problems of ceramic-based SOFCs, such as poor sealing, mechanical issues, and thermal shock vulnerabilities. The metal-supported SOFC cells developed by H&Power shows excellent mechanical strength, good thermal shock resistance, and easy sealing compared with conventional ceramic-based cells. The resulting design is currently at the cell-stack level and is considered to be a realistic possibility for APU applications for heavy duty trucks
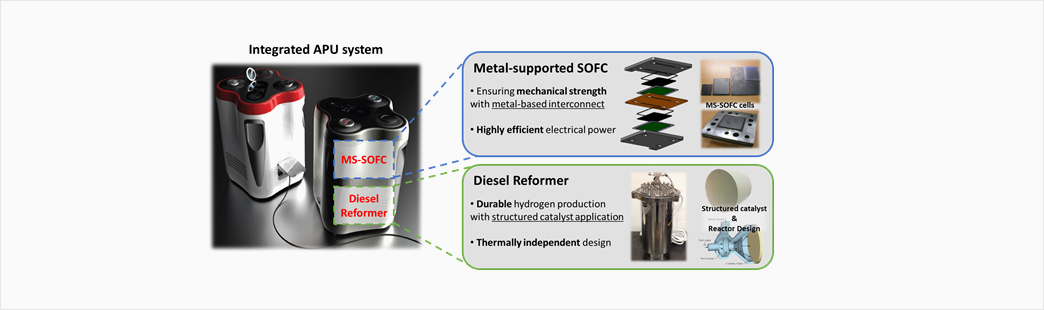
Although there are promising expectations for an SOFC-based APU system, the major problem with the current system is due to unstable system performance. To gain long-term performance, the issue regarding catalyst deactivation due to carbon deposition on the catalyst surface must be resolved. Sulfur and aromatic compounds in the fuel have been identified as the main factors influencing carbon deposition in the diesel reformer. The number of active sites on the catalyst is diminished by sulfur poisoning and by the formation of carbon. Additionally, aromatic compounds are usually converted to olefins such as ethylene, which is a typical precursor of carbon formation. The SOFC also incurs a carbon deposition problem at the anode when using hydrocarbons as a fuel. Mechanical strength, thermal shock resistance, and sealing are the other major issues that must be dealt with before SOFCs are feasible for wider commercial use.
APU Project at the Saudi Aramco-KAIST CO2 Management Center
Saudi Aramco, a Saudi Arabian national petroleum and natural gas company, has created the Saudi-Aramco-KAIST CO2 Management Center at the KAIST campus in Daejeon. The center's main goal is finding solutions to carbon management and one of the funded projects deals with SOFC-based APUs for heavy-duty trucks. From previous research projects between Saudi Aramco and KAIST, fuel injectors and post processors were introduced to maintain stable reforming. The integrated diesel reformer was successfully operated for 2500 hours (for the first time in the world). Also, a structured catalyst was developed for a 1kW pre-reforming reactor. Using design factors from previous research projects, a 1kW diesel reformer was fabricated for the APU project. The project will deliver a first-of-its-kind APU system with a metal-supported SOFC that will be utilized. In terms of the overall efficiency and durability, the prototype will demonstrate the clear benefits of a diesel reformer and metal-supported SOFC system over the ceramic SOFC APU using commercial diesel.
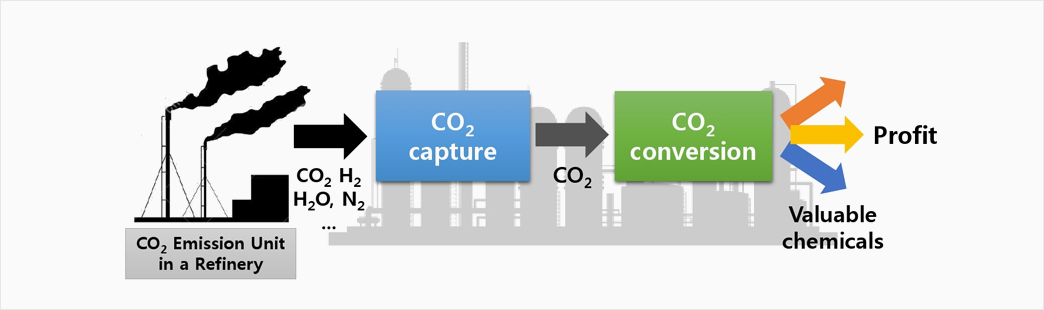